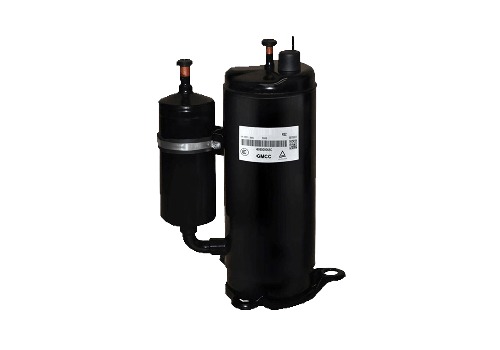
Introduction
Reciprocating compressors are the unsung heroes of many industrial processes. These powerful machines play a crucial role in various sectors, from oil and gas to manufacturing and refrigeration. In this blog post, we’ll dive into the world of reciprocating compressors, exploring their functionality, applications, and importance in modern industry.
What is a Reciprocating Compressor?
A reciprocating compressor, also known as a piston compressor, is a positive-displacement machine that uses pistons driven by a crankshaft to deliver gases at high pressure. The name “reciprocating” comes from the back-and-forth motion of the piston within a cylinder.
How Does It Work?
The operation of a reciprocating compressor can be broken down into four main steps:
- Suction: As the piston moves downward, it creates a vacuum in the cylinder, drawing gas in through the inlet valve.
- Compression: The piston then moves upward, compressing the gas within the cylinder.
- Discharge: Once the gas reaches the desired pressure, the discharge valve opens, and the compressed gas is expelled.
- Expansion: The piston moves back down, and the cycle repeats.
Applications of Reciprocating Compressors
Reciprocating compressors find use in a wide range of industries:
- Oil and Gas: For natural gas compression and transportation
- Petrochemical: In various refining processes
- Manufacturing: Powering pneumatic tools and equipment
- Refrigeration: In cooling systems for industrial and commercial use
- Pharmaceutical: For producing medical-grade gases https://youtu.be/XUa0LsaoGjU?si=ITDJjC44b716dVPr
- Advantages of Reciprocating Compressors
- High Pressure Capability: Can achieve very high discharge pressures
- Flexibility: Easily adjustable to varying load conditions
- Efficiency: High efficiency, especially at lower flow rates
- Durability: Long operational life with proper maintenance
Challenges and Maintenance
While reciprocating compressors are robust, they require regular maintenance:
- Valve Maintenance: Valves are subject to wear and need periodic inspection and replacement
- Lubrication: Proper lubrication is crucial for smooth operation and longevity
- Vibration Control: Monitoring and controlling vibration is essential to prevent damage
The Future of Reciprocating Compressors
As industry demands continue to evolve, so do reciprocating compressors. Future trends include:
- Increased Energy Efficiency: Development of more energy-efficient designs
- Smart Technology Integration: Incorporation of IoT and predictive maintenance capabilities
- Environmental Considerations: Design improvements to reduce emissions and environmental impact
- https://youtu.be/AMyNU21ZDp0?si=DtMlr4w8gd500-Xd
Conclusion
Reciprocating compressors remain a vital component in many industrial processes. Their ability to deliver high-pressure gas efficiently and reliably ensures their continued relevance in the face of technological advancements. As we move forward, these powerhouses of compression will undoubtedly continue to play a crucial role in driving industrial progress.