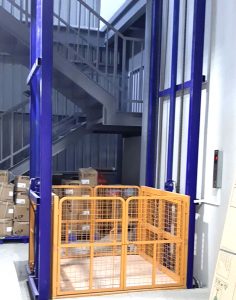
Ever wondered how those smooth-riding elevators in low-rise buildings work?
Meet the hydraulic elevator—a silent workhorse that’s been lifting us up (and down) for decades. Unlike their cable-suspended cousins, hydraulic elevators use the power of fluid mechanics to effortlessly transport passengers and cargo.
But here’s the catch: while hydraulic elevators are marvels of engineering, they’re not without their challenges. Energy efficiency concerns and potential environmental impacts have put these systems under scrutiny in recent years. So, are hydraulic elevators still a viable option in our eco-conscious world?
In this post, we’ll dive deep into the world of hydraulic elevators. We’ll explore their inner workings, safety features, and ideal applications. We’ll also tackle the environmental considerations and maintenance needs that come with these powerful lifting systems. Whether you’re a building manager, an engineering enthusiast, or simply curious about the mechanics behind your daily vertical commute, buckle up for an enlightening journey into the realm of hydraulic elevators.
Understanding Hydraulic Elevators
How hydraulic elevators work
Hydraulic elevators operate using a simple yet effective principle: fluid power. A hydraulic cylinder, filled with oil, pushes a piston that raises and lowers the elevator car. When the elevator needs to ascend, an electric pump forces oil into the cylinder, extending the piston and lifting the car. To descend, a valve releases the oil, allowing gravity to lower the car smoothly.
Types of hydraulic elevators
There are three main types of hydraulic elevators:
- Direct plunger
- Hole-less
- Roped hydraulic
Type | Description | Best for |
Direct plunger | Cylinder directly connected to elevator car | Low-rise buildings |
Hole-less | Telescoping pistons above ground | Medium-rise buildings |
Roped hydraulic | Uses both hydraulics and cables | Taller buildings (up to 8 floors) |
Advantages over traditional cable elevators
Hydraulic elevators offer several benefits compared to their cable counterparts:
- Lower initial installation costs
- Reduced overhead space requirements
- Smoother ride quality
- Easier maintenance
- Higher weight capacity
Key components of a hydraulic elevator system
A hydraulic elevator system consists of several crucial components:
- Hydraulic cylinder and piston
- Oil reservoir
- Electric pump
- Control valve
- Elevator car and guide rails
- Machine room equipment
These components work together to ensure the safe and efficient operation of the elevator. The hydraulic system’s simplicity contributes to its reliability and ease of maintenance, making it a popular choice for many industrial and commercial applications.
Now that we’ve covered the basics of hydraulic elevators, let’s explore their safety features in the next section.
Safety Features of Hydraulic Elevators
Regular Maintenance Requirements
Regular maintenance is paramount for the safe operation of hydraulic elevators. Here’s a list of key maintenance tasks:
- Inspection of hydraulic fluid levels and quality
- Checking for leaks in the hydraulic system
- Testing of safety devices and controls
- Lubrication of moving parts
- Examination of cables and pulleys
Adhering to a strict maintenance schedule not only enhances safety but also prolongs the elevator’s lifespan and improves its efficiency.
Overload Protection Mechanisms
Hydraulic elevators are equipped with sophisticated overload protection systems to prevent accidents and equipment damage. These mechanisms include:
Mechanism | Function |
Load sensors | Detect when the elevator exceeds its weight capacity |
Pressure relief valves | Release excess hydraulic pressure to prevent system failure |
Automatic leveling | Ensures the elevator car is level with the floor, reducing trip hazards |
When an overload is detected, the elevator will typically refuse to move and alert passengers to reduce the load before operation can resume.
Emergency Braking Systems
In the unlikely event of a hydraulic system failure, emergency braking systems provide a crucial safety net. These systems typically include:
- Automatic brakes that engage if the elevator begins to descend too quickly
- Manual lowering valves that allow technicians to safely lower the elevator in case of power failure
- Backup power systems to ensure the elevator can reach the nearest floor during an outage
These emergency features work in tandem to ensure passenger safety under all circumstances, making hydraulic elevators a reliable choice for various applications.
Next, we’ll explore the diverse applications and ideal use cases for hydraulic elevators, showcasing their versatility in different settings.
Applications and Ideal Use Cases
Hydraulic elevators offer versatile solutions for various applications, making them an excellent choice in specific scenarios. Let’s explore the ideal use cases for these robust and efficient lifting systems.
A. Accessibility solutions for existing buildings
Hydraulic elevators are particularly well-suited for retrofitting older buildings with accessibility solutions. Their compact design and minimal overhead requirements make them ideal for structures where space is limited. Here’s why they excel in this application:
- Easy installation in confined spaces
- Minimal structural modifications required
- Cost-effective solution for low-rise buildings
Feature | Benefit for Existing Buildings |
Compact design | Fits in tight spaces |
Low overhead | Minimal roof alterations need |
Simple installation | Reduces construction time and costs |
B. Heavy-duty industrial elevators
In industrial settings, hydraulic elevators shine as heavy-duty lifting solutions. Their robust construction and powerful hydraulic systems make them perfect for handling heavy loads in manufacturing plants, warehouses, and other industrial facilities.
- Capable of lifting substantial weights
- Smooth operation even with uneven load distribution
- Ideal for freight and cargo transportation
C. Low-rise buildings and structures
Hydraulic elevators are the go-to choice for low-rise buildings, typically up to 5-6 stories. Their efficiency and cost-effectiveness in this range make them popular for:
- Small to medium-sized office buildings
- Multi-story parking garages
- Residential apartment complexes
Key advantages for low-rise applications include:
- Lower initial installation costs compared to traction elevators
- Reduced maintenance requirements
- Energy-efficient operation for short travel distances
With these applications in mind, it’s clear that hydraulic elevators play a crucial role in various sectors. Next, we’ll examine the environmental considerations associated with these versatile lifting systems.
Environmental Considerations
As we delve into the environmental aspects of hydraulic elevators, it’s crucial to understand their impact and potential for eco-friendly improvements.
A. Comparison with electric elevators
When it comes to environmental impact, hydraulic and electric elevators have distinct differences:
Feature | Hydraulic Elevators | Electric Elevators |
Energy Consumption | Higher at startup | Lower overall |
Materials | Require hydraulic fluid | No hydraulic fluid need |
Space Requirements | Compact machine room | Larger machine room |
Maintenance | Less frequent | More frequent |
Hydraulic elevators generally consume more energy during startup but require less frequent maintenance, which can reduce the overall environmental impact over time.
B. Eco-friendly hydraulic fluids
To address environmental concerns, manufacturers have developed eco-friendly hydraulic fluids:
- Biodegradable oils
- Vegetable-based fluids
- Synthetic esters
These alternatives reduce the risk of soil and water contamination in case of leaks, making hydraulic elevators more environmentally responsible.
C. Energy efficiency of hydraulic elevators
While traditionally less energy-efficient than their electric counterparts, modern hydraulic elevators have seen significant improvements:
- Variable frequency drives (VFDs) for smoother operation and reduced energy consumption
- Regenerative systems that capture and reuse energy during descent
- Smart control systems that optimize elevator usage and reduce idle time
These advancements have narrowed the energy efficiency gap between hydraulic and electric elevators, making hydraulic options more viable for environmentally conscious building owners.
Next, we’ll explore the installation and maintenance aspects of hydraulic elevators, which play a crucial role in their long-term performance and environmental impact.
Installation and Maintenance
Cost Considerations for Long-term Operation
When considering hydraulic elevators, it’s essential to evaluate the long-term operational costs. While initial installation costs may be lower compared to other elevator types, hydraulic systems can have higher energy consumption over time. Here’s a breakdown of cost factors:
Cost Factor | Description |
Energy Usage | Higher due to hydraulic pump operation |
Fluid Replacement | Periodic replacement of hydraulic fluid |
Seal Maintenance | Regular inspection and replacement of seals |
Environmental Compliance | Costs associated with proper fluid disposal |
Common Maintenance Issues
Hydraulic elevators require regular maintenance to ensure safe and efficient operation. Some common issues include:
- Fluid leaks from seals or pipes
- Worn or damaged cylinder packing
- Air in the hydraulic system
- Contaminated hydraulic fluid
- Malfunctioning valves or controls
Regular inspections and preventive maintenance can mitigate these issues and extend the elevator’s lifespan.
Installation Process and Timeline
The installation of a hydraulic elevator typically involves the following steps:
- Site preparation and hoistway construction
- Installation of the hydraulic cylinder and piston
- Placement of the elevator car and guide rails
- Installation of the hydraulic power unit
- Wiring and control system setup
- Testing and commissioning
The timeline for installation can vary but it generally takes 4-6 weeks for a standard hydraulic elevator.
Space Requirements for Hydraulic Systems
Hydraulic elevators have specific space requirements that differ from other elevator types. Key considerations include:
- Machine room: Typically located adjacent to the hoistway, housing the hydraulic power unit
- Pit depth: Generally shallower than traction elevators, but varies based on travel distance
- Overhead clearance: Less overhead space required compared to traction systems
Now that we’ve covered the installation and maintenance aspects, it’s clear that hydraulic elevators offer unique advantages and considerations for building owners and facility managers.
Hydraulic elevators offer a reliable and efficient solution for vertical transportation in various settings. From their robust safety features to their wide-ranging applications, these elevators provide a cost-effective option for low to mid-rise buildings. While they may have some environmental considerations, proper maintenance and modern design improvements can mitigate these concerns.
As you consider your elevator needs, weigh the benefits of hydraulic systems against other options. Their simplicity, smooth operation, and lower installation costs make them an attractive choice for many projects. Whether you’re planning a new building or upgrading an existing one, consult with a professional elevator company to determine if a hydraulic elevator is the right fit for your specific requirements.