Heat exchangers play a crucial role in low-nitrogen boilers, ensuring efficient thermal transfer and optimal performance. These essential components have a significant impact on the overall efficiency and environmental footprint of boiler systems. Selecting the right heat exchanger is a critical decision that can affect long-term operational costs, energy efficiency, and emissions reduction.
To choose the best heat exchanger for low-nitrogen boilers, several key factors need consideration. This article explores the fundamentals of heat exchangers in these specialized boilers, discusses crucial selection criteria, and examines methods to evaluate heat exchanger performance. Additionally, it touches on important aspects such as maintenance and cleaning to ensure long-lasting efficiency and reliability in low-nitrogen boiler operations.
Understanding Heat Exchangers in Low Nitrogen Boilers
Heat exchangers are essential components in low-nitrogen boilers, designed to transfer heat between different media efficiently. These devices play a crucial role in enhancing the overall efficiency of boiler systems while helping to reduce harmful emissions. In the context of low-nitrogen oxide (NOx) condensing boilers, heat exchangers are particularly important for reclaiming waste heat from flue gasses that would otherwise be released into the atmosphere.
Types of Heat Exchangers
There are several types of heat exchangers used in industrial applications, each with its own unique design and functionality:
- Indirect Heat Exchangers: These keep the cooled and heated fluids separate, with heat exchange occurring across a physical barrier 2.
- Counter-flow Heat exchangers: considered the most effective method of heat exchange, these allow heated and cooling fluids to enter from opposite ends of the device, maximizing efficiency.
- Shell and Tube Heat Exchangers: This design consists of a collection of tubes enclosed within a pressurized outer shell, channeling one fluid through smaller tubes and another through the outer shell 2.
- Plate Heat Exchangers: Composed of several thin plates arranged in stacks, these create channels for fluid flow. Variations like plate-fin exchangers allow for multiple fluid streams.
- Double Pipe Thermal Exchangers: These consist of two concentric pipes, with fluids circulating in opposite directions for maximum efficiency.
How Heat Exchangers Reduce NOx Emissions
Heat exchangers in low NOx boilers contribute significantly to reducing emissions through several mechanisms:
- Efficient Heat Recovery: By recovering waste heat from flue gasses, heat exchangers enable boilers to operate at lower temperatures, reducing thermal NOx formation.
- Condensation Process: Low NOx condensing boilers can condense water vapor in flue gasses, releasing additional latent heat. This process, facilitated by heat exchangers, can result in efficiency levels exceeding 90%.
- Optimized Combustion: Effective heat exchange allows for better control of combustion temperatures, which is crucial for minimizing NOx formation.
Efficiency Benefits
The incorporation of advanced heat exchangers in low-nitrogen boilers offers several efficiency benefits:
- Enhanced Overall Efficiency: By reclaiming waste heat, these systems can achieve efficiency levels often exceeding 90%, translating to lower fuel costs and reduced greenhouse gas emissions.
- Lower Operating Temperatures: Heat recovery allows boilers to operate at lower temperatures, reducing thermal stress on components and minimizing the risk of corrosion and wear.
- Improved Lifespan: The typical lifespan of a heat exchanger often aligns with that of the boiler, which can be between 15 and 20 years.
- Real-time Optimization: Modern heat exchangers incorporate sensors and controls for real-time monitoring of temperature and pressure, allowing for performance optimization based on actual conditions 1.
By leveraging these advanced heat exchanger technologies, low-nitrogen boilers can significantly reduce their environmental impact while maintaining high operational efficiency.
Key Factors in Selecting a Heat Exchanger
Material Considerations
When selecting materials for heat exchangers, several factors need careful consideration. Thermal conductivity is paramount, as materials with high conductivity, such as copper, aluminum, and brass, are more effective at transferring heat. Corrosion resistance is equally crucial, especially in environments with corrosive elements like chlorides or hydrogen sulfide. The chosen material must be compatible with the fluids it will contact to prevent premature deterioration.
Cost is another significant factor, as high-performance materials like copper can be expensive for certain applications. Fabrication considerations are also important, as some materials are more challenging to work with, impacting overall cost and lead time.
Size and capacity
The size and capacity of a heat exchanger are critical factors in its selection. An ideal boiler plant should have a minimum of two units for the heating load, with a third for redundancy 2. The goal is to have 3-5 heat exchangers to meet the heating load effectively. Using different equipment sizes can be beneficial, but there’s a diminishing return to increasing the number of units due to maintenance costs and space requirements 2.
Turndown capacity is crucial because boiler plants are designed for the coldest days of the year, which account for less than 1% of total runtime. Most of the time (over 50%), the boiler plant operates at significantly reduced input during colder months 2. High turndown in condensing boilers translates directly to fuel savings, as they are more efficient at lower firing rates.
Pressure Drop and Flow Rate
Pressure drop is a critical factor in heat exchanger design, affecting both performance and efficiency. It occurs when fluid enters one end of the heat exchanger and leaves the other, often due to restrictions or blockages in the flow. 3. Higher velocities result in increased pressure drop, which is directly related to heat transfer coefficients. 3. The optimal design balances the lowest possible pressure loss with the highest heat transfer coefficient.
To optimize pressure drop, designers can consider several factors:
- Baffle selection: Proper choice of baffles can help manage turbulence and pressure drop 3.
- Tube pitch and pattern: A higher pitch results in lower pressure drop and turbulence 3.
- Nozzle size: Proper selection ensures less pressure loss 3.
- Number of passes: A higher number of passes increases pressure drop 3.
Maintaining minimum velocities is essential, especially over the lifespan of the upstream facility 4. Additionally, fouling characteristics, cleaning needs, plot availability, and exchanger approach temperature are key considerations in heat exchanger selection and operation 4.
Evaluating Heat Exchanger Performance
Thermal efficiency metrics
Thermal efficiency is a crucial metric for evaluating heat exchanger performance in low-nitrogen boilers. It measures how effectively the heat exchanger transfers heat from the combustion process to the water or steam. This efficiency is expressed as a percentage, calculated by dividing the output energy by the input energy and multiplying by 100 1. However, thermal efficiency alone does not provide a complete picture of boiler performance, as it only considers the heat exchanger’s effectiveness 1.
A more comprehensive measure is fuel-to-steam efficiency, which can be calculated using two methods: the input-output method and the energy balance method 1. The input-output method divides the boiler output by the input, both measured in BTUs, while the energy balance method subtracts actual losses from an ideal 100% efficiency 1.
Fouling Resistance
Fouling, the formation of unwanted deposits on heat transfer surfaces, significantly impacts heat exchanger performance. It creates an insulating layer that reduces heat transfer efficiency and increases energy consumption. The fouling factor, expressed as Rd = 1/Ud – 1/U, quantifies this impact on overall heat transfer coefficient 3.
To mitigate fouling, several strategies can be employed:
- Material selection: Using corrosion-resistant materials like 304 or 316 stainless steel for plates, pipes, and tubes can reduce fouling.
- Maintaining constant flow: uniform fluid flow across heat transfer surfaces helps prevent particulate accumulation.
- Backflushing: Reversing fluid flow can dislodge particulates at the exchanger inlet 2.
- Port filtration: Preventing particles from entering the unit reduces fouling potential 2.
Maintenance Requirements
Regular maintenance is essential for optimal heat exchanger performance. Monitoring temperature and pressure is crucial for detecting fouling and other issues. 2. Cleaning frequency depends on the specific application and fouling rate, but regular cleaning is vital for maintaining efficiency.
The proper flow rate during cleaning ensures effective mechanical action of fluids. Additionally, monitoring stack temperature helps assess heat transfer efficiency, as higher flue gas temperatures indicate less effective heat transfer.
By focusing on these key areas—thermal efficiency, fouling resistance, and maintenance—operators can ensure their heat exchangers maintain peak performance in low-nitrogen boiler applications.
Conclusion
Choosing the right heat exchanger for low-nitrogen boilers has a significant impact on overall system efficiency and environmental performance. By carefully considering factors such as materials, size, capacity, and pressure drop, operators can optimize their boiler systems to achieve higher thermal efficiency and reduced emissions. This approach not only leads to cost savings but also contributes to a more sustainable operation in the long run.
To wrap up, regular evaluation and maintenance of heat exchangers are crucial to ensuring their continued performance. By monitoring thermal efficiency metrics, addressing fouling issues, and sticking to a proper maintenance schedule, operators can extend the lifespan of their equipment and maintain peak efficiency. These practices, combined with thoughtful selection, enable businesses to make the most of their low nitrogen boiler systems, balancing operational needs with environmental responsibilities.
FAQs
- How should one select the appropriate heat exchanger for their needs?
To choose the right heat exchanger, you should evaluate several key factors, including the unit’s performance, ease of maintenance, cost considerations, pressure drops, and the characteristics of the fluids involved to ensure optimal functionality. - What considerations are important when determining the size of a heat exchanger?
Determining the correct size for a heat exchanger involves considering the temperatures, flow rates, and types of fluids involved. A commonly used guideline is to select a heat exchanger with a surface area 1.5 to 2 times greater than the calculated heat transfer area. - Which type of heat exchanger is most suitable for boilers?
Aluminum heat exchangers are highly recommended for boilers due to their lightweight and superior heat transfer capabilities. The variety of aluminum alloys available further enhances their suitability, making them a popular choice for wall-hung boilers. - What criteria should be used to choose a specific heat exchanger for a particular application?
When selecting a heat exchanger for a specific application, consider the pressure, temperature, and corrosiveness of the fluids involved, as well as the required heat transfer area and efficiency. Also, take into account the space available for installation, ease of maintenance, and both initial and ongoing costs.
References
[1]- https://burnertec.com/low-nox-burner-an-introduction/
[2] – https://www.ipieca.org/resources/energy-efficiency-database/heat-exchangers-2022
[3] – https://www.enerquip.com/3-benefits-of-low-nox-heaters/
[4] – http://www.tkycglc.cn/en/Case/20160814/94.html
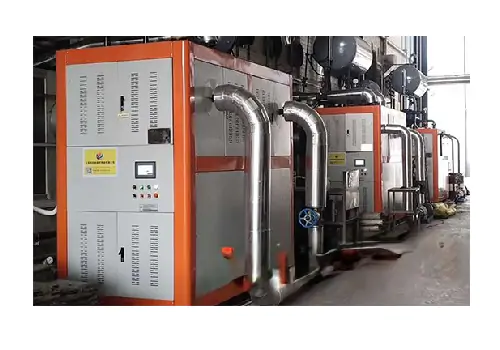